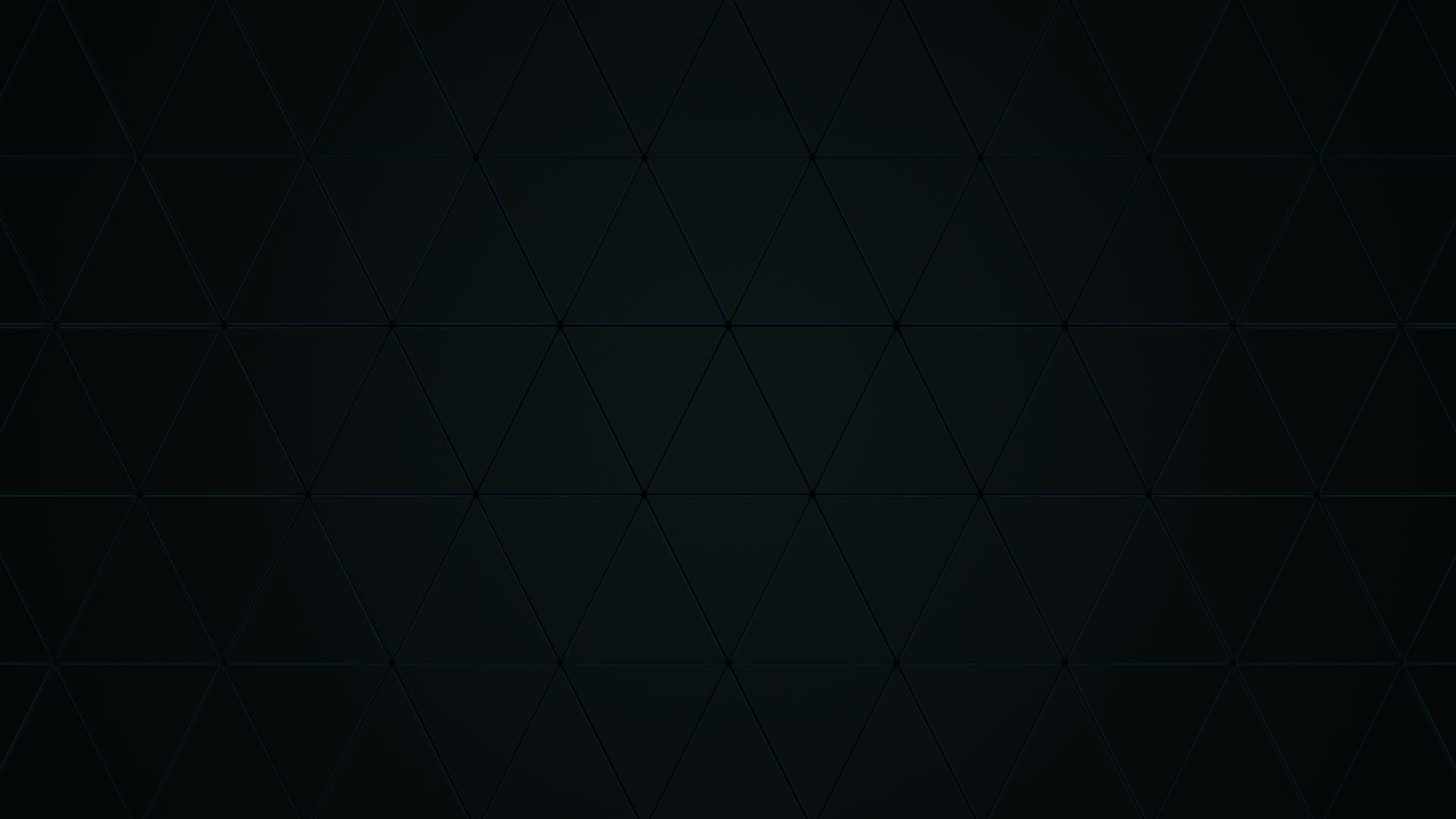
TECHNOLOGIES

Pour une création unique WGP réalise des cadres en fibre de carbone aux propriétés exceptionnelles. Ce résultat est le fruit de longues et minutieuses recherches des ingénieurs en collaboration avec les manufactures les plus compétentes et les mieux qualifiées.
Soucieux de vous apporter des produits performants en qualité et fiabilité, et afin d’être à la hauteur des grandes marques de cycles présentes sur le marché, WGP utilise les matériaux indispensables et adaptés provenant de ces établissements de réputation reconnue.
WGP va vous instruire sur toutes les étapes nécessaires à la réalisation de nos cadres en fibre de carbone.

Cette fibre se distingue de la HMF par des performances et des caractéristiques nettement supérieures.
Elle est plus légère, plus résistante à la torsion et à la déformation. Elle offre 20% supplémentaires en rigidité que la HMF. Cette intensification est dispensée dans les zones déterminées nécessaires.
La combinaison créée pour la HMF+ est étudiée et développée pour répondre aux exigences de diminution du poids.
Les filaments de la HMF+ sont de diamètre inférieur rendant 14% plus léger le cadre que la HMF. Cette fibre utilisée notamment dans la structure des avions commerciaux permet une plus grande absorption des chocs et une transmission de la puissance optimisée.
Fibre aux caractéristiques remarquables : fiabilité, résistance, faible poids et rendement performant.
La rigidité obtenue assure le bon équilibre entre le confort recherché et les bonnes sensations grâce à une meilleure flexibilité. Ce procédé de fabrication nous permet de mieux exploiter les qualités de cette fibre de module standard.
La fabrication de nos cadres en carbone commence par le choix de fibres de qualité. Nos spécialistes dotés d’un savoir-faire professionnel avéré combinent idéalement les fibres sur les parties du cadre afin de respecter parfaitement les zones de confort et de rigidité soigneusement déterminés au préalable par les ingénieurs. Cela permet la transmission de la puissance développée par le coureur sans entrainer une perte de rendement et rendre agréable la position et le pédalage sur le vélo.
Pour arriver à ce résultat WGP a choisi d’utiliser trois types de conception de fibres de carbone réunies avec la résine « Epoxy Matrix » la mieux adaptée et la plus employée pour ses propriétés d’assemblage et de collage des fibres entre elles qui favorisent la très grande résistance du carbone.
Cette association résine plus carbone nous assure ainsi une production fiable et stable.
LA FIBRE DE CARBONE



Toujours à la recherche de performances WGP emploie aussi la fibre HMU issue de l’industrie de l’aérospatiale. Ce type de fibre est utilisé pour la compétition de haut niveau, c’est-à-dire que nous mettons entre vos mains la meilleure technologie en place.
Elle est composée de fibres MGR60H qui apportent 30% en plus de résistance à la traction que la fibre HMF+. La réalisation en multicouche donne aussi une meilleure capacité d’absorption des vibrations et plus de longévité aux produits. Ses filaments sont de diamètre inférieur et rendent plus léger le cadre de 8,5% qu’avec la HMF+. Le résultat final permet l’obtention d’un cadre avec une rigidité maximale et un poids plume.
MATERIEL EMPLOYE
LES MATERIAUX COMPOSITES

EPOXY RESIN PROCESS
Nous associons la technologie nano CNT. Les nanotubes de carbone améliorent la résistance du composite. En combination avec (Matrice Epoxy) la résine époxy on obtient une plus grande résistance à la rupture de 49% par rapport à la résine standard et 20% plus élevée que dans le cas de la nanotechnologie ordinaire. La technologie CNT permet également une réduction significative du risque de fissure et une durée de vie beaucoup plus longue tout en réduisant le poids.
Les matériaux composites des cadres en carbone se composent principalement de l’alliage de la fibre avec la résine. La résine Epoxy est plus chère que les autres mais offre de biens meilleurs résultats en termes de rigidité, de résistance et longévité.
PROCEDE DE FABRICATION
Toutes nos fibres de très haute qualité et tous les avantages liés à leur utilisation ne serviraient à rien sans des procédés de fabrication respectant scrupuleusement toutes les normes rigoureuses et essentielles pour réaliser cadre en carbone. Nous optimisons constamment nos procédés et vérifions chaque pièce avant qu’elle ne quitte notre usine.
Nos exigences nous amènent à respecter ces normes du début jusqu’à la fin.
1. Création design et ingéniérie
Les cadres WGP sont pensés et créer à partir de logiciel industriel de design qui permettent de déterminer avec précision les parties du cadre où les efforts créés seront les mieux reproduit afin d'optimiser la performance de l'athlète.
2. Découpe des fibres de carbon
WGP utilise des machines pour découper les fibres de carbone qui permettent de réduire les pertes et de garantir une découpe précise, respectant ainsi parfaitement l’orientation des fibres préalablement choisi et d’obtenir un poids minimal. Cela nous permet de conserver les qualités des fibres et donc les sensations procurées par le vélo.
3. Réassemblage des fibres de carbone
4. Application des feuilles de carbone imprégnées de la résine époxy sur chaque tube
Nous rassemblons plus de 220 pièces de carbone pour la fabrication d’un cadre alors que d’autres marques n’utilisent qu’en moyenne que 110 pièces.
Les feuilles de carbone sont disposées à la main sur chaque tube avec la résine epoxy.
5. Introduction du moule dans le four
Une fois les fibres de carbone bien orientées, nous introduisons le moule dans le four pour permettre au contact de la résine epoxy, lors du séchage, de rigidifier et rendre plus résistant la structure de carbone.
6. Assemblage des tubes
7. Test de contrôle qualité
8. Peinture et vernissage
9. Positionement des autocollants
10. Dernier test et contrôle de qualité du produit fini avant envoi
TEST ET CONTRÔLE DE LA QUALITE

Notre détermination pour la qualité nous a ammené à travailler avec des fournisseurs et fabricants qui répondent aux normes ISO9001 et AS/EN/JIS9100 (dernière en vigueur) et ISO4210 / EN / SGS ce qui nous oblige à la mise en œuvre d’un processus en amélioration permanente.
A l’écoute de la clientèle jusqu’à sa satisfaction nos fournisseurs et fabricants ont mis en place des structures qui englobent particulièrement :
Des tests en laboratoire validant la régularité des matières premières et des produits.
Des vérifications sérieuses à chaque phase de la production.
Une complète traçabilité des matériaux et des procédés avec des comptes rendus de laboratoire.
La compétence en qualité de WGP BICYCLE COMPONENTS a été reconnue par l’appréciation de nos clients et par les organismes certificateurs.
De plus WGP Bicycle Components tire bénéfice de l’assistance des centres de recherche et développement des manufactures dont les technicités de pointe apportent dans le domaine du cycle.
Avant la mise en production nous exécutons une batterie de tests d’après les nouvelles normes DIN EN 14781 et 14766 . En outre nous testons par paliers allant du plus faible vers plus dur notre propre essai. Nous utilisons des forces allant jusqu’à 15KGs sur les bouts des cintres qui fléchissent de 30mm. Pendant les essais en production nous faisons évoluer tous nos produits au niveau du poids et de la sécurité.
TECHNOLOGIE APPLIQUEE


Toute la technologie Aero permet de gagner un maximum de vitesse tout en optimisant sa consommation d'energie. Inspiré de l'aviation et des recherches réalisé par le NACA, les cadres WGP bénificiant des dernières avancés technologiques Aerodynamic Science permettent d'optenir un profil aérodynamique unique et novateur afin de repousser les limites de l'effort face au vent.

Nos ingénieurs développent des cadres ultra léger pour garantir toujours plus de performance et de confort sur le vélo. Obtenir un cadre ultra léger permet certes plus de facilité lors des montés mais les cadres Ultra Light Frame WGP Bicycle Components apportent pas seulement un poids réduit; avec la fibre de carbone 60 tons ils garantissent une rigidité du cadre conservée lors du pédalage pour permettre une transmission de la puissance optimale. Tout le savoir-faire WGP Bicycle Components permet de combiner la légèreté à l'extrême maniabilité et d'obtenir la rigidité souhaitée tout en respectant nos exigences de procédé de fabrication.




ADVANCED RACING TECHNOLOGY définie l'essence même de WGP. Cela résume toute l'expérience que WGP Bicycle Components apporte à ces fabrications. Elle est issue de son expérience du cyclisme professionnel retransmis dans le développement de ces produits émanant des dernières technologies les plus avancés du marché. Tous le savoir-faire et la vision WGP permet de garantir des produits de haute qualité.






Pour ne pas avoir de perte de rendement lors de la transmission de la puissance pendant le pédalage et offrir une rigidité maximale, nous renforçons, grâce au procédé Cross Weave System, les parties du cadre au niveau du tube de direction et du boîtier de pédalier par des bandes de carbone tissées en croiser. Cela permet d'obtenir une rigidité exceptionnelle en torsion et ainsi d’assurer toute la transmission de la puissance de pédalage.






Le passage des câbles de frein et de dérailleur s'insère par l'intérieur du cadre leur garantissant plus de protection pour une meilleur durabilité face à la corrosion et la saleté tout en apportant plus d’élégance au cadre.












